Noise protection for all
machines in bottling technology
<
BEVERAGES
FOOD
PHARMACEUTICAL
-
tried and tested
-
extreme noise level reduction
-
optimal ease of operation
-
no production interference
-
stainless steel version
noise protection enclosure for separator
The machines in bottling companies are known to emit noise levels to a considerable level
above the mandatory limits.
Product range
Complete programme
- secondary noise protection casings
on every machine in bottling technology
(e.g. conveyors, fillers, packers,
cleaning machines, unscrewer,
inspectors, packaging machines)
- protection casings
We give advice on site.
In the bottling- and packaging industry the requirements for (protection) noise protection are varied and equipment specific.
A specialist can show you the best solution for your project directly on site.
HEIN Noise Protection has been your competent partner for over 25 years.
Proof of high technical standards are the best reference.
HEIN - the authority in noise protection
complete casing for an unloader
mobile protection casing for initial weight scale
unscrewer casings
noise protection casing for packer
noise protection for palletisers and de-palletisers
noise protection for de-palletisers
total enclosure of a labelling machine
noise protection for bottle plate in a pharmaceutical company
noise protection enclosure for paper cup machines
Version: SPECIAL
Version: SPECIAL
Subject to the quite critical constructive necessity (infeed of dirty bottles below the clean bottle output) with single-end machines HEIN has undertaken special development efforts in this respect.
In the application of the SPECIAL version (European patent) the clean bottles area is separated from the dirty bottle infeed below (see system drawing).
Thus, besides the excellent noise level reduction a significant contribution to the prevention of (re)-infection of the discharged clean bottles is achieved in addition!
The great advantage was not only recognised by a well-known machine manufacturer, but also by users, and therefore, this system is especially popular with the application of critical products, if for other reasons double-end machines are dispensed of.
Antiseptic installations (head room disinfection) could provide the safe prevention of reinfection of the clean containers - from the last flush to the discharge - in the critical area inside the cleaning machines.
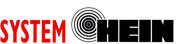
cam plate open
total covering (closed) of a bottle cleaning machine
noise protection covering of a single-end machine
(discharge side only)
Machine Model: KASKANA
Year of manufacture 1990
noise protection fairing for a double-end machine (discharge side) model: LAVANA 1991
pneumatic operation
noise protection coverng for a single-end machine
total covering for a double-end machine (here insert)
|